3D Anode for Electric Transportation/Aviation
Battery has become critical component in our daily lives – from our smartphone, laptop to electric vehicle/transportation. We need our batteries to have capacity to hold more power, longer, lighter and cheaper. To achieve higher power capacity, but lighter and cheaper, one crucial component in the battery cell is the anode.
The best design for battery anodes in the Lithium-Ion Battery (LIB) is 3D lattice structure such as shown in the figure below. The 3D lattice structure – especially when it is in nano or micrometer scales – allows the highest surface to volume ratio which then leads to max power per unit weight.
The issue is the cost. Most fabrication methodologies involve using very sophisticated equipment and thus expensive. Our team at Oregon Renewable Energy Center (OREC) pioneers a low-cost method – enabled by Additive Manufacturing – in producing these 3D microlattice structures for next-generation LIB so our smart phones could hold more power longer but cheaper. And TESLA’s electric vehicles could be the Volkswagen of our era – the vehicle for the mass.
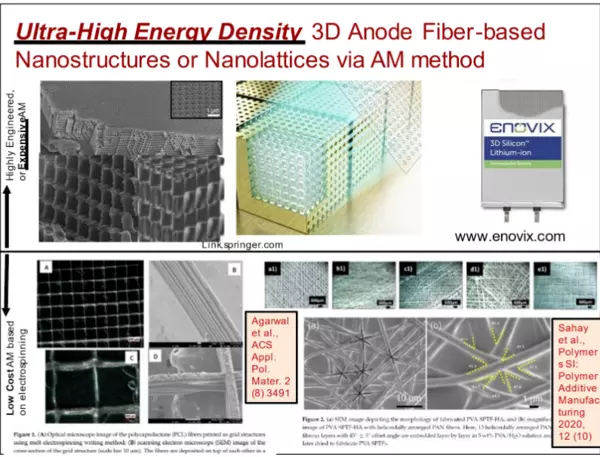
Anode design is a crucial factor for the further development of lithium-ion battery (LIB) technology, especially in terms of achieving the high charging rate performance, as typically needed in electric vehicles (EV) and electric transportation/aviation. 3D nanostructures have been identified as the key to dramatically enhanced charging rate of LIB, in addition to the change of materials (from carbon-based anode to silicon-based). However, existing fabrication methodologies for 3D nanostructures are inherently expensive – using advanced lithography techniques or other nanopatterning methodologies, as well as using additive manufacturing approaches. Electrospinning (as an integrated additive manufacturing methodology) may be used to produce low-cost 3D-printed fiber structures. Our joint collaboration team has done groundwork in this field of research in the past 3-4 years, which would allow the extension of this special additive manufacturing approach to reach nanoscale 3D-printed fiber structures more economically and with scalability for manufacturing. This would pave the way to achieve the order of magnitude increase in battery charging rate as needed to realize the vision of the electrification of mobility/transportation.
This research proposal aims to realize the potential for next generation battery performance by building the prototype of the 3D nanostructures anode, validating its optimum design capacity by computational modeling/simulation and finally, integrating the novel anode design into real, working LIB device. The targeted output of this research program includes the above engineering prototypes that will be useful for further implementation in the industry, along with journal publications and other forms of dissemination of the new knowledge and innovations into the world scientific communities. This research program will be built on the team’s existing groundwork in electrospinning-based additive manufacturing (Es-AM). The technology will be further developed into manufacturing methodology that will be ready for pilot-line/semi-high volume LIB product implementation in the industry – Technology Readiness levels of 4-6.
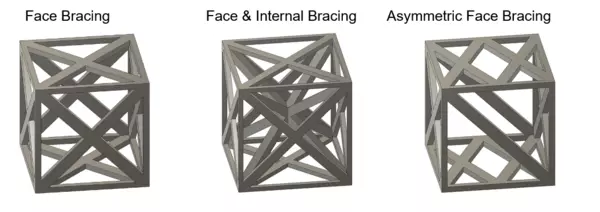
INTRODUCTION
While cathode has been the subject of active research for the cutting-edge development of Li-ion battery (LIB) technology globally, anode has recently gained importance as the key component for next-generation LIB. In addition to the regular battery performance parameters such as capacity, energy density, lifetime, etc., charging rate has been identified as a critical parameter of an energy storage performance [1-3]. It is especially crucial to enable the vision of the Electric Vehicle (EV) – charging electric car after all should not be much longer than filling up gas in the petrol station [3].
Key to this high charging rate performance is the anode design and technology (structures, geometries, etc.), in addition to the material itself [4-5]. Today’s mainstream lithium ion batteries have used graphite as anode material as it exhibits several optimal qualities, such as structural stability and low electrochemical reactivity (with respect to lithium ions). Some forms of the carbon-based materials that have been widely used as anode for commercial batteries include mesocarbonmicrobead (MCMB), artificial and natural graphite, carbon fiber or C-C composites material [6], carbon nanotube, and also graphene [7]. The basic idea here was to design carbon-based anode structures and geometries that maximizes the kinetics of the Li intercalation and diffusion. 3D nanostructures have thus been identified as the ultimate anode design for high charging rate performance [8-12]. However, existing fabrication methodologies for 3D nanostructures are prohibitively expensive – using advanced lithography techniques or other nanopatterning methodologies [13-16].
Electrospinning (as an integrated additive manufacturing methodology) has been effective in producing cheap 3D-printed fiber structures [17-18]. Unlike traditional AM (Additive Manufacturing) techniques, electrospinning allows definition of individual fibers (dimensions, architectures, etc.) but produce them in batches (ie. not individually, which makes regular AM very expensive, takes a long time to integrate into real engineering systems). But so far Es-AM (electrospinning-based additive manufacturing) produces largely random 3D fiber structure and not nanoscale [17-18]. Only this year (2020), our group (joint collaboration between Singapore University of Technology & Design and La Trobe University, Australia) just reports successful fabrication of 3D fiber-based nanostructures – ie. sub-micron fibers (several hundreds of nm) aligned densely and uniformly (not random) and stacked layer to layer and finally forming 3D nanolattices/grid structures [19-20]. This was enabled by a clever modification of the deposition platform of the Es-AM technique, such as reported in our most recent publication, essentially self-assembling and self-stretching the fibers into the smaller scales [20]. Thus, by further engineering of the methodology, we may reasonably expect to achieve real nanometer scaled fibers (~tens of nm). Such low-cost 3D nanostructures could pave the way to high charging rate battery performance, while allowing mass production and scalability.
This research proposal specifically aims to develop the prototype of the 3D nanostructures anode (with fiber diameter in ~tens of nm range; max ~100 nm within the experimental uncertainty limitations), validating its optimum design capacity by computational modeling/simulation (fiber/pitch dimensions, 3D structures – lattices vs. helicoidal, for instance) and finally, integrating the novel anode design into real, working LIB device (charging/discharging cycles).
LITERATURE REVIEW
Energy storage became an essential requirement in modern electric vehicle systems, portable electronic gadgetry, solar and wind farms etc. There are several energy storage systems (batteries) available at different sizes and capacities however, lithium-ion battery (LIB) has been proven to be the most promising candidate because of its several qualities such as high efficiency, high energy density, limited self-discharge, longer life cycle even with high charging and discharging rates [21-23], which are important modern battery design parameters. Charging rate performance has most recently become very important and active area of research, and anode design plays key roles in achieving enhanced charging rate [1-5].
A widely explored approach to enhance the charging rate of LIB is to replace the conventional bulk form of graphitic anode with nanostructures [4-5]. For instance, 1D (one dimensional) nanostructures, in the form of nanowires, have been demonstrated with enhanced charging rate [4-5, 24-25]. This is associated with the increase in the rate processes or kinetics of the Li intercalation and diffusion. In addition, nano-structuring was also proven to be effective in relaxing the high strain due to expansion (during charging, large flux of lithium ions absorbed in anode could lead to significant expansion of anode, and thus extremely high mechanical stress which could potentially cause preliminary failure) and increasing the surface area available for the chemical reaction [26-27]. Silicon nanostructures, for instance, were proved to be better than their bulk counter parts in capacity retention [28-30]. Different nanostructures such as nanoparticles, nanospheres, nanowires, nanotubes and nano-cones were experimentally proved to exhibit better cycling life and performance as LIB electrodes [4, 27, 29-39].
3D nanostructures have thus been considered to be the ultimate structural design to maximize the kinetics of the Li intercalation and diffusion into the anode material, and eventually the charging rate performance [8-12]. However, existing fabrication methodologies for 3D nanostructures are inherently expensive – using advanced lithography techniques or other nanopatterning methodologies, as well as using additive manufacturing approaches [13-16]. Nanopatterning is always expensive as it requires nanoscale pattern definition using very high resolution light (with very small wavelengths) or sophisticated laser-based systems. Additive manufacturing has also been used to fabricate 3D nanostructures but as it produces essentially one droplet of materials at a time (ie. not a batch process), it takes very long time generally to integrate into realistic engineering devices and thus production cost would soar.
Fiber-based structures/architectures are an emerging class of materials that are increasingly investigated for a wide range of applications, including biomedical, energy, packaging, and advanced structural applications [40-44]. Among all the processing technologies, electrospinning has gained widespread attention as one of the simplest and straightforward fabrication techniques to produce such fiber-based materials [45,46]. The fibers produced using this technique have a large length to diameter ratio and large surface area. The high draw ratio and elongation experienced by the fibers during the electrospinning process aligns the molecular chains along the fiber axis. This explains why electrospun fibers can display enhanced mechanical strength and stiffness compared its bulk counterparts [47–50].
However, despite the advantages of electrospinning in producing fiber reinforced composites, the use of the conventional electrospinning setup has had limited success in producing controlled three-dimensional architectures. Recently, some studies have explored the melt-electrospinning setup to deposit fibers in a controllable manner [51-53]. In the melt-electrospinning writing setup, the electrospinning voltage and the distance between the electrospinning nozzle and collector are lowered. As the polymer jet ejected from the electrospinning nozzle does not experience whipping instabilities, it ensures that the fibers can be deposited in a precise manner to obtain three-dimensional fiber patterns [52]. Thus, such an electrospinning-based methodology could be considered as an additive manufacturing (AM) approach, as it lays down one fiber materials at a time in a precise and controllable manner [54-55]. With this approach, 3D fiber-based architectures were recently reported and demonstrated using the melt-electrospinning writing set up [19], such as shown in Figure 1. The three-dimensional grid patterns were produced using melt-electrospinning based on polycaprolactone (PCL) material, which was chosen in this study due to its low melting point (~60℃) and thus the compatibility with the melt-electrospinning setup [19]. These three-dimensional fiber grid structures were then embedded in polyvinyl alcohol (PVA) matrix, which was chosen as the matrix material due to its water solubility and ability to form films. Since the fibers were melt extruded out of the nozzle and then deposited on a collector, the surface of the fibers tended to fuse with the fibers on top of which they were deposited. This also ensured that the fibers present at the interconnecting junctions within the grid bind strongly with one another. Embedding these fiber structures within the matrix demonstrated improvement of the structural properties of the architecture [19].
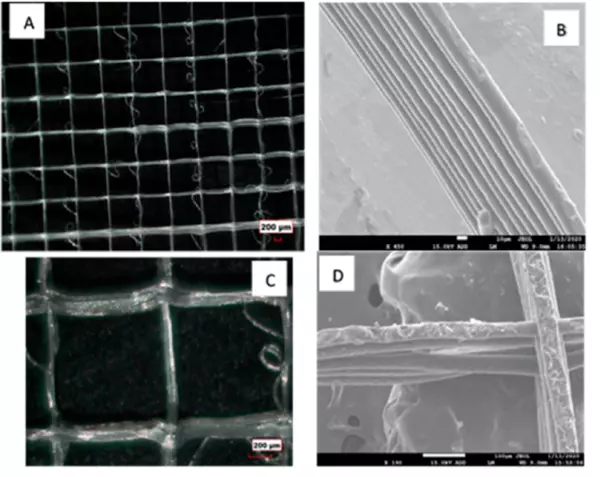
Figure 1. (A) Optical microscope image of the polycaprolactone (PCL) fibers printed as grid structures using melt electrospinning writing method; (B) scanning electron microscope (SEM) image of the cross-section of the grid structure (scale bar 10 μm). The fibers are deposited on top of each other in a controlled manner; (C) optical microscope image of the PCL fibers demonstrating the cross-over points of the grid structures; and (D) SEM image demonstrating the surface morphology of the fibers (scale bar 100 μm) [19].
The above 3D-printed fibers were however in hundreds of micron scales as evident from Figure 1 above, so the 3D grid structures are not nanostructures. Materials with smaller scale (sub-micron down to nanometer) structural features have received wide attention in the past two decades [56–58]. Nanowires [59], nanopillars [60] or bulk materials with nanoscale grain structure [61] or nanolayers [62–65] have shown exciting, unprecedented functional properties, in addition to excellent structural properties. Thus, research has been very active recently to enable fabrication of the structural geometries in the sub-micron/nano level [56,60,66], including in electrospun 3D-printed fiber grid structures. Sahay et al. (2020) [20] has most recently demonstrated the successful fabrication of such 3D structures in the ~1 μm scales, as a further development of the electrospinning-based methodology. Specifically, Sahay et al. (2020) [20] demonstrated the unique use of parallel plates for deposition platform to allow significant improvement in the fiber diameter reduction (from ~ hundreds of μm to ~1 μm range), while maintaining uniform and dense alignment of the fibers. With this set up, further engineering and optimization of the technique may be expected to lead to even further significant (1-2 order/s of magnitudes) reduction in fiber diameters into the tens of nanometer scales.
METHOD
Es-AM (Electrospinning-based Additive Manufacturing) to Create 3D Nanostructures
Within our joint collaboration team, we have the Es-AM rapid prototyping capabilities in Singapore University of Technology & Design (SUTD, Singapore) as well as in La Trobe University (LTU, Australia). Sahay et al. (2020) [20] was based on work done mostly in SUTD. Agarwal et al. (2020) [19] was based on work done in SUTD and LTU. Dr. Rahul Sahay and Ms. Komal Agarwal were Postdoctoral Fellow and Ph.D student, respectively, in SUTD, working under the supervision of both Co-I Arief Budiman (while he was still in SUTD) and Collaborator Avinash Baji (of LTU).
With the current Es-AM set up, the joint collaboration team proposes to conduct further engineering and optimization of the set up to achieve further significant (1-2 order/s of magnitudes) reduction in fiber diameters – into at least the tens of nanometer ranges. Polymer materials such as PCL (polycaprolactone) or PAN (polyacrylonitrile) for the fibrous phases will be used as model materials to demonstrate the feasibility of creating the prototype of 3D fiber-based nanostructures.
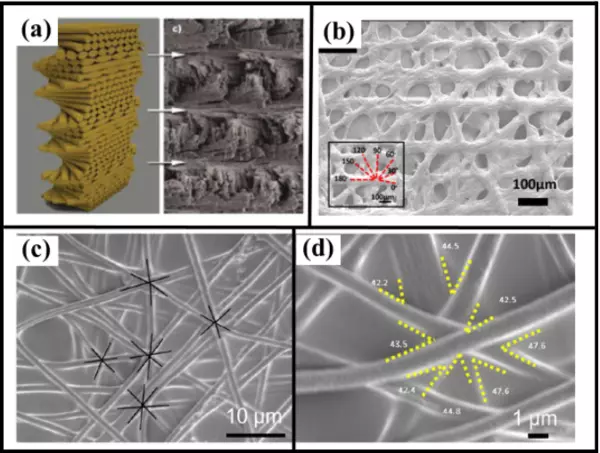
Figure 2. (a) 3D model of helicoidal alignment as well as cross-sectional scanning electron microscope (SEM) image of Odontodactylus scyllarus (Mantis Shrimp)’s dactyl club, the bio-inspiration of the 3D helicoidal architecture [54]; (b) top-view SEM image showing helicoidal fiber alignment (fiber diameters in the ~tens of μm range) [55]; (c) top-view SEM image showing helicoidal fiber alignment (fiber diameters in the single digits to ~1 μm range) [20].
In addition to fiber dimension reduction, the current Es-AM set up that we have developed in the last 3-4 years in SUTD, would also be capable of creating different structural design of the 3D architectures. 3D fiber grid patterns were produced in Agarwal et al. (2020) [19], as illustrated in Figure 1). 3D fiber helicoidal alignment were produced in Sahay et al. (2020) [20] and Agarwal et al. (2019) [54] and a few other references [51,55,67], as further illustrated in Figure 2. These 3D structural architectures may affect substantially the kinetics in lithium ion intercalation and diffusion in LIB device, cycling lifetime/reliability of the anode (associated with stress evolution) as well as structural integrity of overall anode design.
OPTIMIZING THE NOVEL 3D NANOSTRUCTURE ANODE DESIGN
Once the capability to achieve nanoscale 3D-printed fibers is confirmed in the first stage of this research program, the subsequent phase would be the engineering design and optimization of the 3D nanostructure anode. From kinetics point of views, it is obvious that the larger the surface/volume ratio, the processes of lithium ion intercalation and diffusion into the anode would be faster, thus LIB charging rate performance would monotonically increase with fiber size reduction. However, as the fibers become smaller and smaller, the structural integrity or strength of the overall architecture may suffer [68]. Recent reports have also indicated that stress evolution may also lead to less reliability (more preliminary failures/cracks) of the nanostructures, if fibers are too small, although at the same time, the stress self-limiting capability would increase [24-25,28,30]. This phase of the research program aims at the optimum design of the 3D nanostructures – in terms of fiber (and pitch) geometries, as well as structural design of the 3D architectures (grid/lattice vs. helicoidal). The outcome would be the 3D nanostructure anode design that could lead to maximum performance as an LIB device (especially in terms of charging rate), while maintaining reasonable structural integrity and cycling lifetime (reliability) for the anode as an integrated part of the LIB device/system.
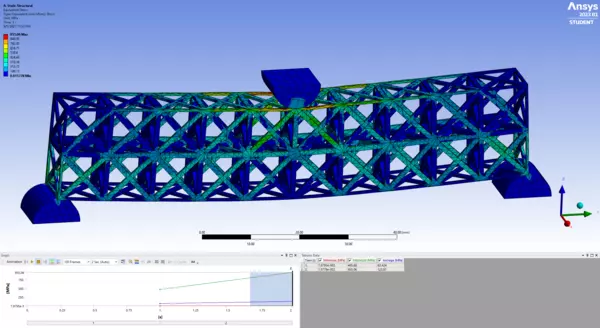
Finite Element Methodology (FEM) will be used to model and simulate all the three factors for engineering design and optimization phase: the kinetics of the lithium ion intercalation and diffusion into the anode material (ie. the lithiation process), the structural integrity/strength of the overall 3D nano-architectures, as well as stress evolution during the lithiation process (which leads to cycling lifetime/reliability). FEM coupled with optimization techniques will be used, such as ANSYS (FEM Package and Optimization), or alternatively optimization algorithms (such as steepest descent algorithm) run on Python or Matlab. AI (Artificial Intelligence) or ML (Machine Learning) methodologies may also be used to accelerate the iterations needed to achieve the global optimum for the anode design. AI and ML would also be used to drive the prediction and invention of completely new 3D architectures based on our modeling/simulation/optimization work here.
INTEGRATION INTO REAL WORKING LITHIUM ION BATTERY (LIB) DEVICES
The final stage is to integrate the optimum 3D nanostructure anode design into a real working LIB device – ready for pilot-line/semi high-volume manufacturing in the industrial setting. Real electrode materials would be needed here for the 3D nanostructure anode. Several electrode materials have been produced using electrospinning methodology and used as anode materials for LIB devices, such as CuO [10] and Carbon [69]. These materials need to be integrated into the current Es-AM set up. Further engineering/optimization of the set up may be needed for use with these materials. Once 3D nanostructure anode using an actual electrode material is achieved, then the team plans to collaborate with industry partner/s to integrate the novel anode prototypes into real working LIB devices. Finally, electrical characterization of the LIB device would be conducted to validate the optimum design and evaluate LIB performance vs. reliability.
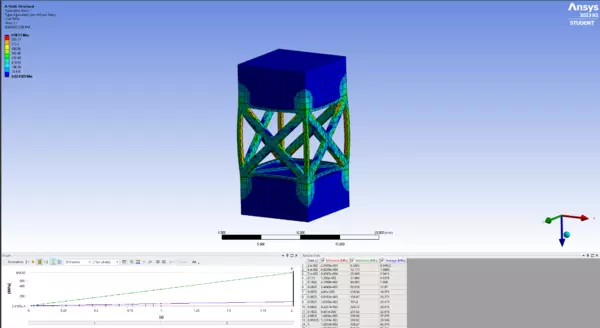
CONCLUDING REMARKS
Anode design is a crucial factor for the further development of lithium-ion battery (LIB) technology, especially in terms of achieving the high energy density as well as extremely fast charging rate performance, as typically needed in electric vehicles (EV) as well as electric transportation/aviation. 3D nanostructures have been identified as the key to dramatically enhanced charging rate of LIB, in addition to the change of materials (from carbon-based anode to silicon-based). Electrospinning (as an integrated additive manufacturing methodology) may be used to produce low-cost 3D-printed fiber structures. In this manuscript, we demonstrate the groundwork in this field of research in the past 3-4 years, which would allow the extension of this special additive manufacturing approach to reach nanoscale 3D-printed fiber structures more economically and with scalability for manufacturing. This would pave the way to achieve the orders of magnitude increase in battery energy density and charging rate as needed to realize the vision of the electrification of mobility/transportation, especially in aviation.
Stay tuned for more updates!
Important Vocabulary
Nano – A measurement at 1/1,000,000 of a meter
Advanced Lithiography – A technique of printing and imaging/viewing extremely small features
Nanopatterning Methodologies – A method of producing a product at a nanoscale size
Electrospinning - A production method to create incredibly fine fibers using an electric force that interacts with the electrons in polymers
Technology Readiness Scale – A method of determining the maturity of a technology from 1 to 9
Dissemination – The act of spreading something
Cathode – the electrode where a current exits the battery
Electrochemical Reactivity – A chemical reaction triggered by a significant voltage difference
Meso carbon microbead – An anisotropic small bead that gets separated by the matrix from the solvent
Anisotropic – A property of a material that allows it to change its properties or shape
Intercalation – to insert something between layers of a crystal lattice
Polycaprolactone – a biodegradable polyester with a low melting point
Poly Vinyl Alcohol – a water soluble synthetic polymer
Matrix Material – a material that provides the composite its shape; reinforces the fibers
Kinetics – a form of chemistry that studies rates of reactivity
Monotonically – a function varying in a way that never increases or decreases
Anode – an electrode where the current enters the battery
[1] N. Omar, M. Daowd, P. v. d. Bossche, O. Hegazy, J. Smekens, T. Coosemans, and J. v. Mierlo, “Rechargeable energy storage systems for plug-in hybrid electric vehicles - Assessment of electrical characteristics,” Energies, vol. 5, no. 8, pp. 2952-2988, 2012.
[2] S. M. Lukic, J. Cao, R. C. Bansal, F. Rodriguez, and A. Emadi, “Energy storage systems for automotive applications,” IEEE Transactions on industrial electronics, vol. 55, no. 6, pp. 2258-2267, 2008.
[3] L. H. Saw, Y. Ye, and A. A. Tay, “Integration issues of lithium-ion battery into electric vehicles battery pack,” Journal of Cleaner Production, vol. 113, pp. 1032-1045, 2016.
[4] C. K. Chan, H. Peng, G. Liu, K. McIlwrath, X. F. Zhang, R. A. Huggins, and Y. Cui, “High-performance lithium battery anodes using silicon nanowires,” Nature nanotechnology, vol. 3, no. 1, pp. 31-35, 2008.
[5] J.-Y. Li, Q. Xu, G. Li, Y.-X. Yin, L.-J. Wan, and Y.-G. Guo, “Research progress regarding Si-based anode materials towards practical application in high energy density Li-ion batteries,” Materials Chemistry Frontiers, 2017.
[6] S. Hossain, Y.-K. Kim, Y. Saleh, and R. Loutfy, Comparative studies of MCMB and C-Ccomposite as anodes for lithium-ion battery systems,J Power Sources,114, 264–276,(2003).
[7] Y. Abu-Lebdeh and I. Davidson, inNanotechnology for Lithium-Ion Batteries, 117–162,Springer, Canada
[8] P.G. Bruce, B. Scrosati, J.M. Tarascon, Angew. Chem., Int. Ed. 2008, 47, 2930−2946.
[9] A.S. Arico, P. Bruce, B. Scrosati, J.M. Tarascon, W. van Schalkwijk, Nat. Mater. 2005, 4, 366−377.
[10] R. Sahay, P.S. Kumar, V. Aravindan, J. Sundaramurthy, W.C. Ling, S.G. Mhaisalkar, S. Ramakrishna, S. Madhavi, “High Aspect Ratio Electrospun CuO Nanofibers as Anode Materials for Lithium Ion Batteries with Superior Cycleability,” Journal of Physical Chemistry C, vol.116, pp. 18087-18092, 2012.
[11] T.D. Hatchard, J.M. Topple, M.D. Fleischauer, J.R. Dahn, Electrochem. Solid-State Lett. 6 (2003)
[22] M.D. Fleischauer, M.N. Obrovac, J.R. Dahn, Electrochem. Solid-State Lett. 155(2008) A851eA854.
[13] J. Suk, D.Y. Kim, D.W. Kim, Y.K. Kang, J. Mater. Chem. A 2 (2014) 2478e2481.
[14] C.D. Wang, Y.S. Chui, R.G. Ma, T.L. Wong, J.G. Ren, Q.H. Wu, X.F. Chen,W.J. Zhang, J. Mater. Chem. A 1 (2013) 10092e10098.
[15] Y.Y. Tang, X.H. Xia, Y.X. Yu, S.J. Shi, J. Chen, Y.Q. Zhang, J.P. Tu, Electrochim.Acta 88 (2013) 664e670.
[16] X. Wang, L. Sun, R.A. Susantyoko, Y. Fan, Q. Zhang, Nano Energy 8 (2014)71e77
[17] S. Coppola, G. Nasti, V. Vespini, P. Ferraro, Layered 3D Printing by Tethered Pyro-Electrospinning, Advances in Polymer Technology, Volume 2020, Article ID 1252960.
[18] W. Chen, Y. Xu, Y. Li, L. Jia, X. Mo, G. Jiang, G. Zhou. 3D printing electrospinning fiber-reinforced decellularized extracellular matrix for cartilage regenerationChemical Engineering Journal 382 (2020) 122986
[19] K. Agarwal, R. Sahay, A. Baji. Tensile Properties of Composite Reinforced with Three-Dimensional Printed Fibers Polymers 2020, 12, 1089; doi:10.3390/polym12051089
[20] R. Sahay, K. Agarwal, A. Subramani, N. Raghavan, A.S. Budiman, A. Baji. Helicoidally Arranged Polyacrylonitrile Fiber-Reinforced Strong and Impact-Resistant Thin Polyvinyl Alcohol Film Enabled by
Electrospinning-Based Additive Manufacturing Polymers 2020, 12, 2376; doi:10.3390/polym12102376
[21] N. Omar, M. Daowd, P. v. d. Bossche, O. Hegazy, J. Smekens, T. Coosemans, and J. v. Mierlo, “Rechargeable energy storage systems for plug-in hybrid electric vehicles - Assessment of electrical characteristics,” Energies, vol. 5, no. 8, pp. 2952-2988, 2012.
[22] S. M. Lukic, J. Cao, R. C. Bansal, F. Rodriguez, and A. Emadi, “Energy storage systems for automotive applications,” IEEE Transactions on industrial electronics, vol. 55, no. 6, pp. 2258-2267, 2008.
[23] L. H. Saw, Y. Ye, and A. A. Tay, “Integration issues of lithium-ion battery into electric vehicles battery pack,” Journal of Cleaner Production, vol. 113, pp. 1032-1045, 2016.
[24] I. Ali, S. K. Tippabhotla, I. Radchenko, A. Al-Obeidi, C.V. Stan, N. Tamura, A.S. Budiman, Probing Stress States in Silicon Nanowires during Electrochemical Lithiation using In Situ Synchrotron X-Ray Microdiffraction. Frontiers in Energy Research. 6; 19, 2018. DOI: 10.3389/fenrg.2018.00019
[25] S. K. Tippabhotla, I. Radchenko, C. V. Stan, N. Tamura and A.S. Budiman. Stress Evolution in Silicon Nanowires during Electrochemical Lithiation Using In Situ Synchrotron X-ray Microdiffraction, J. Mater. Res. 34, p.1622-31, 2019
[26] P. G. Bruce, B. Scrosati, and J. M. Tarascon, “Nanomaterials for rechargeable lithium batteries,” Angewandte Chemie International Edition, vol. 47, no. 16, pp. 2930-2946, 2008.
[27] M.-H. Park, M. G. Kim, J. Joo, K. Kim, J. Kim, S. Ahn, Y. Cui, and J. Cho, “Silicon nanotube battery anodes,” Nano letters, vol. 9, no. 11, pp. 3844-3847, 2009.
[28] S. W. Lee, M. T. McDowell, L. A. Berla, W. D. Nix, and Y. Cui, “Fracture of crystalline silicon nanopillars during electrochemical lithium insertion,” Proceedings of the National Academy of Sciences, vol. 109, no. 11, pp. 4080-4085, 2012.
[29] X. H. Liu, L. Zhong, S. Huang, S. X. Mao, T. Zhu, and J. Y. Huang, “Size-dependent fracture of silicon nanoparticles during lithiation,” Acs Nano, vol. 6, no. 2, pp. 1522-1531, 2012.
[30] I. Ryu, J. W. Choi, Y. Cui, and W. D. Nix, “Size-dependent fracture of Si nanowire battery anodes,” Journal of the Mechanics and Physics of Solids, vol. 59, no. 9, pp. 1717-1730, 2011.
[31] M. V. Shelke, H. Gullapalli, K. Kalaga, M. T. F. Rodrigues, R. R. Devarapalli, R. Vajtai, and P. M. Ajayan, “Facile Synthesis of 3D Anode Assembly with Si Nanoparticles Sealed in Highly Pure Few Layer Graphene Deposited on Porous Current Collector for Long Life Li‐Ion Battery,” Advanced Materials Interfaces, vol. 4, no. 10, 2017.
[32] X. Zhou, Y.-X. Yin, L.-J. Wan, and Y.-G. Guo, “Facile synthesis of silicon nanoparticles inserted into graphene sheets as improved anode materials for lithium-ion batteries,” Chemical communications, vol. 48, no. 16, pp. 2198-2200, 2012.
[33] T. Ma, X. Yu, H. Li, W. Zhang, X. Cheng, W. Zhu, and X. Qiu, “High Volumetric Capacity of Hollow Structured SnO2@ Si Nanospheres for Lithium-Ion Batteries,” Nano Letters, 2017.
[34] H. Ma, F. Cheng, J. Y. Chen, J. Z. Zhao, C. S. Li, Z. L. Tao, and J. Liang, “Nest‐like silicon nanospheres for high‐capacity lithium storage,” Advanced Materials, vol. 19, no. 22, pp. 4067-4070, 2007.
[35] T. Kennedy, M. Brandon, and K. M. Ryan, “Advances in the Application of Silicon and Germanium Nanowires for High‐Performance Lithium‐Ion Batteries,” Advanced Materials, vol. 28, no. 27, pp. 5696-5704, 2016.
[36] H. C. Shim, C.-S. Woo, and S. Hyun, "Silicon-Carbon Nanotube Aerogel Core-Shell Nanostructures for Lithium-Ion Batteries with Long-Cycle Life and High Capacity." pp. 276-276.
[37] S. Zhang, Z. Du, R. Lin, T. Jiang, G. Liu, X. Wu, and D. Weng, “Nickel Nanocone‐Array Supported Silicon Anode for High‐Performance Lithium‐Ion Batteries,” Advanced Materials, vol. 22, no. 47, pp. 5378-5382, 2010
[38] H. Yang, S. Huang, X. Huang, F. Fan, W. Liang, X. H. Liu, L.-Q. Chen, J. Y. Huang, J. Li, and T. Zhu, “Orientation-dependent interfacial mobility governs the anisotropic swelling in lithiated silicon nanowires,” Nano letters, vol. 12, no. 4, pp. 1953-1958, 2012
[39] X. H. Liu, H. Zheng, L. Zhong, S. Huang, K. Karki, L. Q. Zhang, Y. Liu, A. Kushima, W. T. Liang, and J. W. Wang, “Anisotropic swelling and fracture of silicon nanowires during lithiation,” Nano letters, vol. 11, no. 8, pp. 3312-3318, 2011.
[40] Gupta, M.K.; Srivastava, R.K. Mechanical Properties of Hybrid Fibers-Reinforced Polymer Composite:
A Review. Polym. Plast. Technol. Eng. 2016, 55, 626–642.
[41] Sathishkumar, T.P.; Naveen, J.; Satheeshkumar, S. Hybrid fiber reinforced polymer composites—A review.
J. Reinf. Plast. Compos. 2014, 33, 454–471.
[42] Datsyuk, V.; Trotsenko, S.; Trakakis, G.; Boden, A.; Vyzas-Asimakopoulos, K.; Parthenios, J.; Galiotis, C.;
Reich, S.; Papagelis, K. Thermal properties enhancement of epoxy resins by incorporating polybenzimidazole
nanofibers filled with graphene and carbon nanotubes as reinforcing material. Polym. Test. 2020, 82, 106317.
[43] Zhang, L.; Liu, W.; Wen, X.; Chen, J.Y.; Zhao, C.S.; Castillo-Rodriguez, M.; Yang, L.W.; Zhang, X.Q.; Wang, R.; Wang, D.Y. Electrospun submicron NiO fibers combined with nanosized carbon black as reinforcement for multi-functional poly(lactic acid) composites. Compos. Part A Appl. Sci. Manuf. 2020, 129, 105662.
[44] Sessini, V.; Galisteo, A.J.L.; Leones, A.; Urena, A.; Peponi, L. Sandwich-Type Composites Based on Smart
Ionomeric Polymer and Electrospun Microfibers. Front. Mater. 2019, 6, 301.
[45] Wang, G.L.; Yu, D.M.; Kelkar, A.D.; Zhang, L.F. Electrospun nanofiber: Emerging reinforcing filler in polymer matrix composite materials. Prog. Polym. Sci. 2017, 75, 73–107.
[46] Palazzetti, R.; Zucchelli, A. Electrospun nanofibers as reinforcement for composite laminates materials—A
review. Compos. Struct. 2017, 182, 711–727.
[47] Wang, D.; Yu, J.J.; Duan, G.G.; Liu, K.M.; Hou, H. Electrospun polyimide nonwovens with enhanced
mechanical and thermal properties by addition of trace plasticizer. J. Mater. Sci. 2020, 55, 5667–5679.
[48] Duan, G.G.; Liu, S.W.; Hou, H.Q. Synthesis of polyacrylonitrile and mechanical properties of its electrospun
nanofibers. e-Polymers 2018, 18, 569–573.
[49] Li, Y.; Gora, A.; Anariba, F.; Baji, A. Enhanced tensile strength and electrical conductivity of electrospun
polyacrylonitrile Yarns via post-treatment. Polym. Compos. 2019, 40, 1702–1707.
[50] Baji, A.; Mai, Y.W.; Wong, S.C. E_ect of Fiber Size on Structural and Tensile Properties of Electrospun
Polyvinylidene Fluoride Fibers. Polym. Eng. Sci. 2015, 55, 1812–1817.
[51] Agarwal, K.; Zhou, Y.N.; Ali, H.P.A.; Radchenko, I.; Baji, A.; Budiman, A.S. Additive Manufacturing Enabled by Electrospinning for Tougher Bio-Inspired Materials. Adv. Mater. Sci. Eng. 2018, 2018, 1–9.
[52] Brown, T.D.; Dalton, P.D.; Hutmacher, D.W. Direct Writing By Way of Melt Electrospinning. Adv. Mater.
2011, 23, 5651–5657.
[53] Yang, G.H.; Mun, F.; Kim, G. Direct electrospinning writing for producing 3D hybrid constructs consisting of
microfibers and macro-struts for tissue engineering. Chem. Eng. J. 2016, 288, 648–658.
[54] K. Agarwal, R. Sahay, A. Baji and A.S. Budiman. Biomimetic Tough Helicoidally Structured Material through Novel Electrospinning-based Additive Manufacturing, Mater. Res. Soc. Adv. 1-10 (2019), Available Online DOI:
[55] K. Agarwal, R. Sahay, A. Baji and A.S. Budiman. Impact-Resistant and Tough Helicoidally Aligned Ribbon Reinforced Composites with Tunable Mechanical Properties via Integrated Additive Manufacturing Methodologies, ACS Appl. Polymer Mater. 2 (8), 3491-3504 (2020)
[56] Nix WD, Gao H (1998) Indentation size effects in crystalline materials: a law for strain gradient plasticity. J Mech Phys Solids 46:411–425
[57] Greer JR, Oliver WC, Nix WD (2005) Size dependence of mechanical properties of gold at the micron scale in the absence of strain gradients. Acta Mater 53:1821–1830
[58] Greer JR, De Hosson JTM (2011) Plasticity in small-sized metallic systems: Intrinsic versus extrinsic size effect. Prog Mater Sci 56:654–724
[59] Budiman AS, Nix WD, Tamura N, et al (2006) Crystal plasticity in Cu damascene interconnect lines undergoing electromigration as revealed by synchrotron x-ray microdiffraction. Appl Phys Lett 88:233515
[60] Budiman AS, Han SM, Greer JR, et al (2008) A search for evidence of strain gradient hardening in Au submicron pillars under uniaxial compression using synchrotron X-ray microdiffraction. Acta Mater 56:602–608
[61] Lu K, Lu L, Suresh S (2009) Strengthening materials by engineering coherent internal boundaries at the nanoscale. Science (80- ) 324:349–352
[62] Radchenko I, Anwarali HP, Tippabhotla SK, Budiman AS (2018) Effects of interface shear strength during failure of semicoherent metal–metal nanolaminates: An example of accumulative roll-bonded Cu/Nb. Acta Mater 156:125–135
[63] Ali HPA, Radchenko I, Li N, Budiman A (2018) The roles of interfaces and other microstructural features in Cu/Nb nanolayers as revealed by in situ beam bending experiments inside an scanning electron microscope (SEM). Mater Sci Eng A 738:253–263
[64] Ali HPA, Budiman A (2019) Advances in In situ microfracture experimentation techniques: A case of nanoscale metal–metal multilayered materials. J Mater Res 34:1449–1468
[65] Tippabhotla SK, Radchenko I (2016) Synchrotron X-ray micro-diffraction–Probing stress state in encapsulated thin silicon solar cells. Procedia Eng 139:123–133
[66] Jiang S, Chen Y, Duan G, et al (2018) Electrospun nanofiber reinforced composites: A review. Polym Chem 9:2685–2720
[67] Chen, R.; Liu, J.; Yang, C.; Weitz, D.A.; He, H.; Li, D.; Chen, D.; Liu, K.; Bai, H. Transparent Impact-Resistant Composite Films with Bioinspired Hierarchical Structure. ACS Appl. Mater. Interfaces 2019, 11, 23616–23622.
[68] X. Zhu, J. Ye, Y. Lu, X. Jia. 3D Graphene Nanostructure Composed of Porous Carbon Sheets and Interconnected Nanocages for High-Performance Lithium-Ion Battery Anodes and Lithium–Sulfur Batteries; ACS Sustainable Chem. Eng. 2019, 7, 13, 11241–11249.
[69] X. Mao, T.A. Hatton, G.C. Rutledge. A Review of Electrospun Carbon Fibers as Electrode Materials for Energy Storage: Current Organic Chemistry 17(13); 2014.